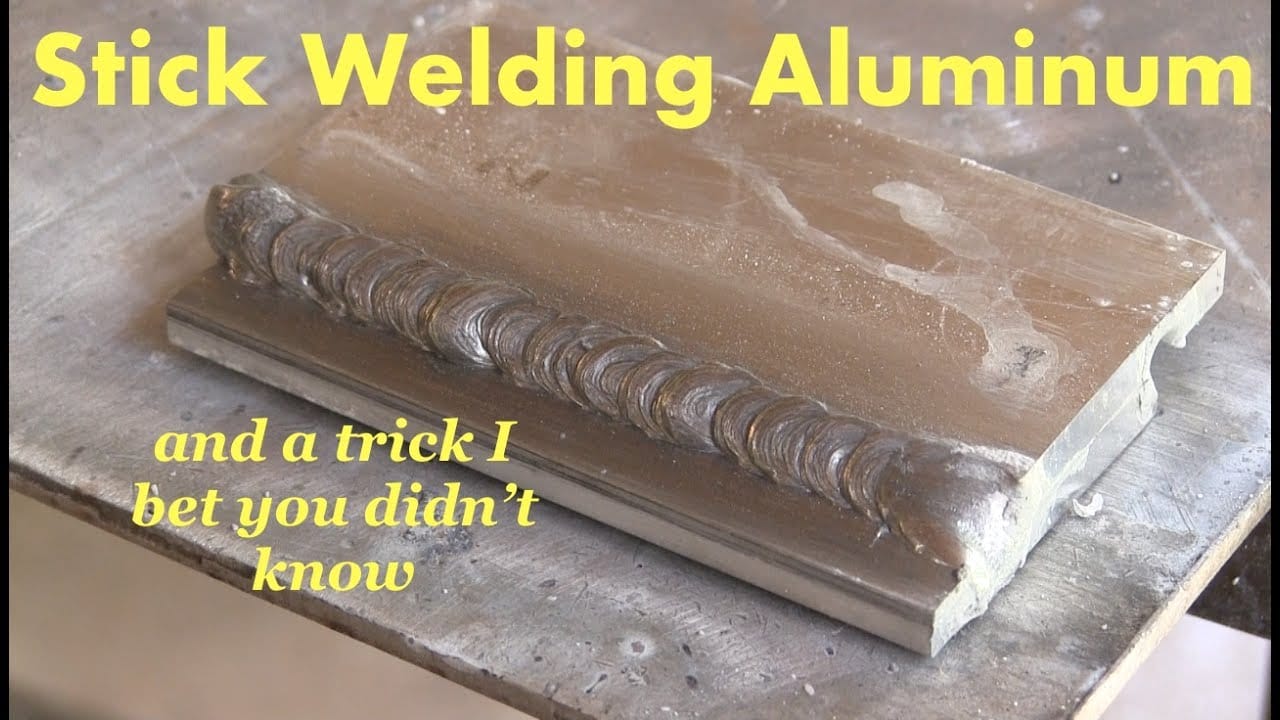
Can you arc weld aluminum? If you’re wondering whether it’s possible to weld this lightweight and versatile metal, you’ve come to the right place! Let’s dive in and explore the fascinating world of aluminum welding together.
Aluminum is used in various industries, from manufacturing to construction, due to its outstanding strength-to-weight ratio. But can you join aluminum pieces together using the arc welding process? Stick around as we uncover the answer and shed light on the possibilities and challenges of welding aluminum.
So, grab your welding helmet and get ready to discover whether you can achieve strong and durable welds on aluminum. Let’s explore the exciting world of aluminum arc welding!
Can You Arc Weld Aluminum?
Arc welding aluminum is possible, but it requires specialized equipment and techniques. Aluminum has a high thermal conductivity and a lower melting point compared to other metals, making it challenging to weld using traditional arc welding methods.
With the right preparation and proper settings, it can be done. It’s important to use AC, clean the surface thoroughly, and choose the correct aluminum electrode. With practice, you can achieve successful aluminum arc welds.
Basics of Aluminum Welding
Aluminum is a lightweight, versatile, and corrosion-resistant metal widely used in various industries. However, unlike steel, aluminum has a significantly lower melting point and higher thermal conductivity, making it more challenging to weld.
Arc welding, specifically Tungsten Inert Gas (TIG) welding, is the preferred method for aluminum welding. TIG welding utilizes a non-consumable tungsten electrode and an inert gas, such as argon or helium, to create the necessary heat and shielding.
What is the Equipment
To successfully arc weld aluminum, you must have the right equipment. Here are the essential tools and materials required:
1. TIG Welder: A TIG welder is specifically designed for aluminum welding. It should have adjustable settings for amperage control to ensure precise heat management.
2. Tungsten Electrode: A non-consumable tungsten electrode is used to create the arc and transfer heat to the aluminum. It should be sharpened to a fine point for better arc stability.
3. Shielding Gas: An inert gas, such as argon or helium, is used to shield the weld pool from atmospheric contamination. Argon is the most commonly used gas for aluminum welding.
4. Filler Rod: Aluminum filler rods are used to add material to the weld joint and create a strong and durable bond. The filler rod should match the type of aluminum being welded.
Arc Welding Process
Arc welding aluminum requires a systematic approach to ensure quality welds. Here’s a step-by-step guide to help you navigate the process:
1. Prepare the Base Metal: Properly clean the aluminum surface to remove any dirt, grease, or oxide layers. Use a stainless steel wire brush or a solvent-based cleaner for effective cleaning.
2. Set Up the Equipment: Connect the TIG torch to the TIG welder and ensure the gas supply is connected and regulated. Choose the appropriate tungsten electrode size and insert it securely into the torch.
3. Adjust the Settings: Set the amperage and balance control on the TIG welder according to the aluminum thickness and desired weld characteristics. Refer to the welder’s manual for specific guidelines.
4. Establish the Arc: Position the tungsten electrode close to the aluminum surface without touching it. Depress the foot pedal or initiate the arc through the control panel to create the arc.
5. Create a Weld Pool: Move the torch slowly along the joint, allowing the heat to melt the aluminum and create a molten weld pool. Maintain proper arc length, usually around 1/8 inch, and control the travel speed for consistent results.
6. Add Filler Metal: As the weld pool forms, introduce the filler rod into the leading edge of the pool. Control the amount of filler metal to prevent excessive build-up or gaps in the weld bead.
7. Complete the Weld: Continue moving the torch along the joint, gradually completing the weld. Maintain a steady hand and ensure proper penetration into the base metal. Use proper techniques to finish the weld and create a visually appealing bead.
Challenges and Benefits of Arc Welding Aluminum
Arc welding aluminum presents unique challenges compared to other metals. However, it also offers distinct benefits that make it a sought-after welding process. Let’s explore some of these challenges and benefits:
Challenges of Arc Welding Aluminum
1. High Thermal Conductivity: Aluminum’s high thermal conductivity means that heat dissipates rapidly, requiring precise heat control to prevent distortion or burn-through.
2. Oxide Formation: Aluminum readily forms an oxide layer on its surface, which must be removed before welding. Failure to remove this oxide layer can result in weak or contaminated welds.
3. Filler Metal Selection: There are various aluminum alloys available, each with different welding characteristics. Choosing the appropriate filler metal for the specific alloy being welded is crucial for achieving optimal results.
Benefits of Arc Welding Aluminum
1. Lightweight and Versatile: Aluminum’s lightweight nature makes it ideal for applications where weight is a factor. It is widely used in the aerospace, automotive, and marine industries.
2. Corrosion Resistance: Aluminum has excellent corrosion resistance, making it suitable for outdoor and marine applications where exposure to moisture and harsh environments is common.
3. Strong and Durable Joints: When properly welded, aluminum joints are strong, durable, and able to withstand high-stress environments. This makes them ideal for load-bearing structures.
While arc welding aluminum may pose unique challenges, it is certainly possible with the right equipment, techniques, and knowledge. By understanding the basics of aluminum welding, selecting the appropriate equipment, and following the step-by-step process, you can achieve quality welds in aluminum.
Embrace the benefits of aluminum as a versatile and lightweight material, and explore the world of aluminum welding with confidence.
Frequently Asked Questions
Here are some commonly asked questions about arc welding aluminum:
1. What is arc welding and how does it work?
Arc welding is a process that uses an electric arc to join metals together. It works by generating intense heat at the welding point, which melts the metal and creates a bond. The electric arc is created by an electrical current passing through an electrode and the metal being welded.
In the case of aluminum, a non-consumable tungsten electrode is typically used in combination with an inert gas, such as argon, to shield the weld from contamination and oxidation.
2. Can you arc weld aluminum?
Yes, it is possible to arc weld aluminum. However, aluminum has different properties compared to other metals, like steel, which can make welding more challenging. Aluminum has a lower melting point and higher thermal conductivity, meaning it requires special techniques and equipment to achieve a successful weld.
Some of the challenges when arc welding aluminum include preventing excessive heat input, managing aluminum oxide layer, and using proper filler materials to achieve a strong and durable weld.
3. What are the advantages of arc welding aluminum?
Arc welding aluminum offers several advantages. One of the main advantages is that it allows for the joining of aluminum parts with a high degree of precision. Arc welding can provide deep penetration and control, resulting in strong and reliable welds.
Arc welding also allows for greater versatility in terms of joint configurations and the ability to weld thicker sections of aluminum. Additionally, arc welding offers the advantage of being a relatively quick and efficient welding process.
4. What are the challenges of arc welding aluminum?
Arc welding aluminum presents several challenges that require careful attention. One of the main challenges is the formation of an aluminum oxide layer on the surface of the metal, which can interfere with the welding process and cause defects in the weld. Proper cleaning and preparation of the aluminum surface before welding are crucial to overcome this challenge.
Another challenge is the high thermal conductivity of aluminum, which can cause rapid heat dissipation and make it difficult to maintain a stable welding arc. Special techniques, such as using high-frequency start or pulsed current, can help overcome this challenge and achieve successful welds.
5. What equipment and techniques are needed for arc welding aluminum?
Arc welding aluminum requires specific equipment and techniques to produce quality welds. Some of the necessary equipment includes a power source capable of producing high-frequency or pulsed current, a tungsten electrode, an inert gas supply for shielding the weld, and a suitable filler material.
Techniques such as proper cleaning and preparation of the aluminum surface, controlling heat input, using the correct welding parameters, and skillful manipulation of the welding torch are essential for successful arc welding of aluminum. Additionally, it is crucial to select the appropriate filler material that matches the composition of the aluminum being welded.
Welding aluminum can be more challenging than welding other metals like steel. This is because aluminum has a lower melting point and conducts heat more effectively, making it prone to warping. However, with the right equipment and technique, it is possible to arc weld aluminum.
To successfully weld aluminum, you will need an AC (alternating current) welding machine, aluminum filler rod, and the correct welding settings. Make sure to clean the aluminum surface thoroughly, use a steady hand, and avoid overheating the metal. Remember, practice makes perfect, so keep trying and don’t get discouraged.