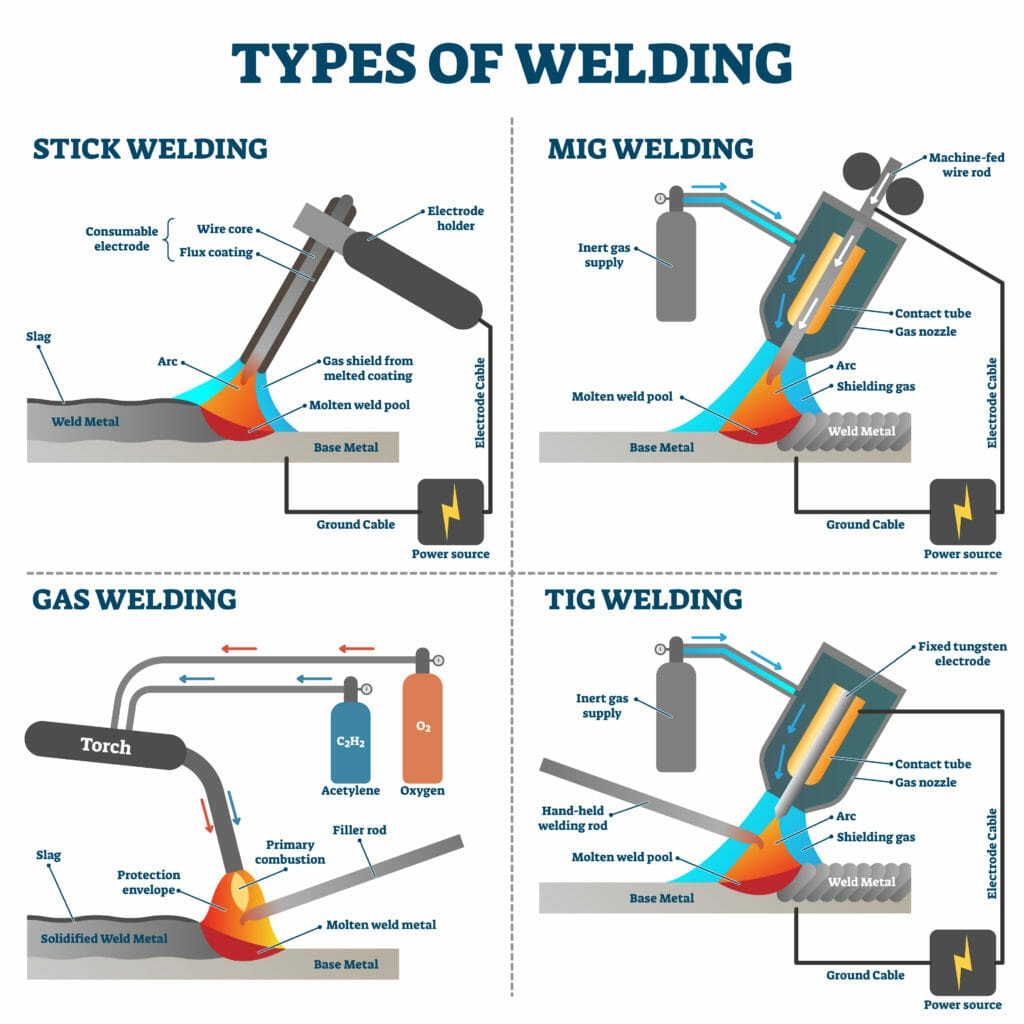
Tig Vs Stick Welding: Get To Know Which Is Right For You?
If you’ve ever been curious about welding, you may have come across the terms “Tig” and “Stick” welding. These are two different techniques used in the welding process, each with its own set of advantages and applications. But which one is right for you? Let’s dive in and find out!
First up, we have Tig welding. Tig stands for tungsten inert gas, and it’s known for its precision and versatility. Tig welding involves using a tungsten electrode to create an arc, which then melts the base metal and a separate filler rod. This process allows for exceptionally clean and aesthetically pleasing welds, making it popular in industries like automotive and aerospace.
On the other hand, we have Stick welding, also referred to as shielded metal arc welding (SMAW). This technique relies on a flux-coated electrode that gets consumed during the welding process. The electric current passes through the electrode, creating an arc that melts the base metal, and the molten metal then solidifies to form the weld. Stick welding is known for its simplicity and versatility, making it a go-to choice for outdoor and heavy-duty applications.
So, which one should you choose? Well, it depends on various factors like the type of material, skill level, and the specific project at hand. Tig welding is ideal for thin and delicate materials, providing precise control and beautiful finishes. Stick welding, on the other hand, is great for thicker materials and rough conditions where portability and durability matter.
Now that you have a basic understanding of Tig and Stick welding, it’s time to explore each technique in more detail and determine which one aligns with your welding needs. So, let’s roll up our sleeves and dive deeper into the fascinating world of welding!
When it comes to choosing between TIG and Stick welding, it’s essential to consider their unique features. In TIG welding, you’ll enjoy precise control and cleaner welds, perfect for thinner metals and artistic work. On the other hand, Stick welding offers better versatility and can handle thicker materials, making it ideal for outdoor projects. The decision ultimately depends on your specific needs and preferences.
Whether you prioritize precision or versatility, understanding the differences between TIG and Stick welding will help you make the right choice.
Tig Vs Stick Welding: Get To Know Which Is Right For You?
When it comes to welding, there are several techniques to choose from, each with its own set of advantages and considerations. Two popular methods are TIG (Tungsten Inert Gas) welding and stick welding. Understanding the differences between these two techniques can help you decide which one is the right fit for your welding projects. In this article, we will explore the intricacies of TIG and stick welding, comparing their features, benefits, and applications.
The Basics of TIG Welding
TIG welding is known for its precision and clean welds. It utilizes a tungsten electrode to create an arc between the electrode and the metal being welded. Unlike stick welding, TIG welding requires the use of shielding gas, typically argon or a mixture of argon and helium, to protect the weld area from atmospheric contamination.
One of the key features of TIG welding is its ability to create welds with exceptional quality and aesthetics. The process allows for greater control over the welding variables, resulting in smoother, cleaner welds that require minimal post-weld cleaning or grinding. This makes TIG welding ideal for applications that demand high visual appeal, such as stainless steel fabrication, automotive restoration, or artistic metalwork.
In addition to its visual appeal, TIG welding offers excellent control over heat input, making it suitable for welding thin materials. The ability to precisely control the heat allows welders to work with delicate materials, such as aluminum, without the risk of distorting or damaging the base metal. TIG welding also enables the inclusion of filler material, which can be added manually to build up welds or reinforce joints.
The Advantages of Stick Welding
Stick welding, also known as Shielded Metal Arc Welding (SMAW), is a versatile welding technique that has been widely used for decades. Unlike TIG welding, stick welding utilizes a consumable electrode coated with flux to create the arc and protect the weld pool from contaminants.
One of the main advantages of stick welding is its versatility. It can be used in various positions, making it suitable for both indoor and outdoor welding applications. This makes stick welding a popular choice for construction sites, pipelines, and structural steel fabrication.
Stick welding is also highly portable, making it a preferred option for fieldwork or remote locations where access to electricity may be limited. The equipment required for stick welding is relatively simple and affordable, making it an accessible option for hobbyists, DIY enthusiasts, or small-scale welding projects.
Key Takeaways: Tig Vs Stick Welding – Get To Know Which Is Right For You?
- Tig welding offers greater precision and control for intricate welding projects.
- Stick welding is more versatile and can be used in various environments and conditions.
- Tig welding produces cleaner and more aesthetically pleasing welds.
- Stick welding is easier to learn and requires less equipment setup.
- Consider the specific requirements of your welding projects to determine which method is best for you.
Frequently Asked Questions
Are you wondering whether TIG or Stick welding is the right choice for your needs? Check out these commonly asked questions to help you decide:
Q1: What are the main differences between TIG and Stick welding?
When it comes to TIG welding, it uses an electric arc formed between a tungsten electrode and the workpiece to create the weld. This process is known for its precision and produces high-quality, clean welds. On the other hand, Stick welding, also known as Shielded Metal Arc Welding (SMAW), involves using a flux-coated electrode that melts into the weld pool, creating a protective shield. Stick welding is versatile and can be used in various environments.
Both processes have their advantages and disadvantages. TIG welding is ideal for working with thin metals and provides excellent control, but it can be time-consuming. Stick welding, on the other hand, is better suited for heavy-duty applications and works well in windy or dirty conditions.
Q2: Which welding process is more suitable for beginners?
If you’re new to welding, Stick welding is often recommended as it has a relatively simple setup and is easier to learn. Stick welding machines are typically more affordable compared to TIG welders, making it a cost-effective option for beginners. Additionally, Stick welding can handle a wider range of metal thicknesses, allowing beginners to practice on various projects without needing multiple setups.
On the other hand, TIG welding requires more skill and finesse, making it a better choice for experienced welders or those who are willing to invest more time into learning the technique. TIG welding is known for its precise control and ability to produce clean, high-quality welds, but it may have a steeper learning curve for beginners.
Q3: Which welding process provides stronger welds?
Both TIG and Stick welding can produce strong welds when done properly. However, TIG welding is often considered to produce stronger welds, especially in applications where precision and aesthetics are important. TIG welding allows for better control over the heat input, resulting in fewer distortions and a more reliable weld.
Stick welding, on the other hand, can also create strong welds when done correctly, but it may have a higher risk of defects such as porosity or slag inclusions. This is why proper technique, including maintaining the correct arc length and electrode angle, is crucial to achieve strong and reliable welds with Stick welding.
Q4: Which welding process is better for thin materials?
If you’re working with thin metals, TIG welding is often the preferred choice. TIG welding allows for precise control of the arc, making it suitable for thin materials that require delicate welds. The ability to adjust the heat input and use filler metals with lower melting points enables TIG welding to create clean, high-quality welds on thin metals.
In contrast, Stick welding may be more challenging for thin materials due to its higher heat input and the nature of the flux-coated electrode. Stick welding can be done on thin materials, but it requires extra care to avoid overheating and causing distortion or burn-through.
Q5: Which welding process is more versatile for different jobs?
If versatility is a key factor for you, Stick welding may be the better option. Stick welding works well in various environments, including outdoor and windy conditions. It can handle different types of joints, positions, and thicknesses, making it suitable for a wide range of welding projects.
TIG welding, while highly precise and producing clean welds, has more limitations in terms of environmental conditions and joint types. TIG welding requires a clean work area and is generally better suited for indoor applications or well-controlled environments. It is commonly used for projects that require high-quality aesthetics, such as stainless steel fabrication or delicate metal artwork.
Summary:
TIG and stick welding are both great options, but they have some key differences. TIG welding is more precise and works well with thin metals, while stick welding is better for thicker materials. TIG welding requires a higher skill level, while stick welding is easier to learn.
In the end, the right choice depends on your specific needs and skill level. If you’re working with thin metals and want precise control, TIG welding might be for you. But if you’re a beginner or working with thicker materials, stick welding could be a better fit. So, consider your needs and go with the welding process that suits you best!