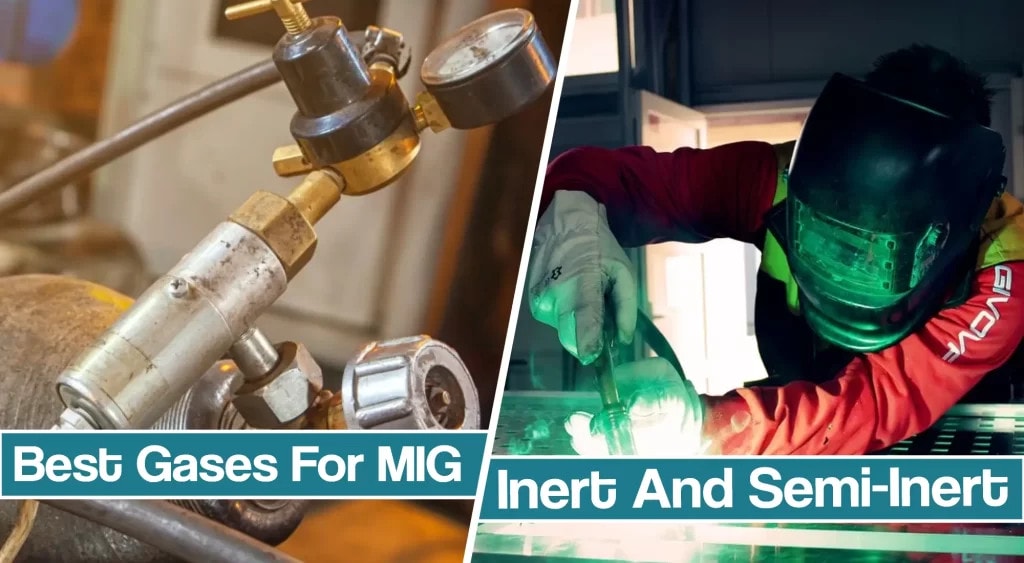
If you’re interested in the world of welding, you’ve come to the right place! Today, we’re going to delve into the exciting topic of “Exploring the Right Gas for MIG Welding.”
Trust me, it’s not as complicated as it sounds. So, buckle up and get ready to discover the key to choosing the perfect gas for your MIG welding needs.
Picture this: you’re in your workshop, sparks flying, and you’re about to tackle an exciting welding project. But wait! Before you dive in, did you know that the gas you use for MIG welding plays a crucial role in achieving top-notch results? Well, it does! In this article, we’ll explore different gases and their unique properties to help you make an informed decision.
So, why is choosing the right gas so important? Well, my friend, the gas you select can affect the stability of your arc, the quality of your weld, and even the overall productivity of your welding process.
No need to panic, though! I’m here to break it down for you and guide you toward finding the perfect gas that suits your welding goals. Let’s get started, shall we?
Exploring the Right Gas for MIG Welding: A Comprehensive Guide
When it comes to MIG welding, choosing the right gas is crucial for optimal results. Different gases offer varying levels of protection, stability, and arc characteristics.
By exploring the various options available, you can find the gas that best suits your welding needs. Consider factors such as cost, availability, and desired weld quality. Knowing the properties and benefits of each gas will ensure a successful MIG welding experience.
Importance of Gas Selection in MIG Welding
When it comes to MIG welding, the type of gas used plays a critical role in shielding the weld pool and preventing oxidization of the metal.
The primary function of the shielding gas is to create a protective atmosphere around the weld area, keeping it free from contaminants and ensuring a clean and strong weld.
Different gases offer varying levels of protection and characteristics, making it essential to choose the right gas based on the materials being welded and desired outcomes.
Role of Argon in MIG Welding
Argon is one of the most commonly used gases in MIG welding, thanks to its excellent inertness and ability to protect the weld from atmospheric gases. With its stable shielding properties, Argon is ideal for welding non-ferrous metals such as aluminum, copper, and stainless steel.
The gas creates a smooth and stable weld pool, with minimal spatter and a clean appearance. Argon also provides good arc stability, making it easier for welders to achieve precise and controlled welds.
Using Argon gas as the primary shielding gas is often recommended when working with non-ferrous metals and for general-purpose welding applications.
It is important to note that Argon is not suitable for welding ferrous materials on its own, as it may contribute to poor penetration and weak welds. In such cases, a blend of gases or a different gas altogether is needed to achieve optimal results.
Versatility of Carbon Dioxide (CO2)
Carbon Dioxide (CO2) is another popular gas used in MIG welding, especially when working with carbon steel. It is more affordable and widely available compared to other gases, making it a cost-effective choice for many welders.
CO2 provides good penetration and high deposition rates, resulting in strong welds. It is particularly suitable for thick material welding, such as structural steel, where high welding speeds are desired.
However, there are some challenges associated with using pure CO2. The gas tends to produce more spatter compared to Argon, making it less suitable for applications that require a clean weld appearance.
CO2 can cause porosity in the weld when used on certain types of metals or in windy conditions. To overcome these limitations, welders often opt for gas blends that combine CO2 with other shielding gases, such as Argon or Oxygen.
Benefits of Using Gas Blends
Gas blends are mixtures of different gases intended to enhance the welding process and optimize the results. These blends are carefully formulated to combine the beneficial properties of each gas, providing superior arc stability, weld appearance, and mechanical properties.
One commonly used gas blend in MIG welding is a mixture of Argon and Carbon Dioxide (ArCO2). This blend offers the best of both worlds by utilizing the stability of Argon and the penetration power of CO2.
It produces cleaner welds with reduced spatter compared to pure CO2 while maintaining good welding speed and deposition rates. ArCO2 blends are versatile and suitable for a wide range of applications, including carbon steel, aluminum, and stainless steel welding.
Choosing the Right Gas for Your Welding Needs
When it comes to selecting the right gas for MIG welding, several factors should be considered. The choice depends on the type of material being welded, the desired weld appearance and properties, the welding process, and even the welding equipment being used.
Consulting with suppliers, and experienced welders, or referring to welding guidelines provided by manufacturers can also help determine the best gas for your specific needs.
To summarize, Argon gas is an excellent choice for non-ferrous metal welding, offering stable shielding and clean welds. Carbon Dioxide (CO2) is ideal for carbon steel welding, providing good penetration and affordability.
Gas blends, such as Argon-CO2 mixes, offer the advantages of multiple gases and are widely used for their versatility. By considering these factors and consulting professionals, you can ensure that you are using the right gas for MIG welding, leading to high-quality welds and improved welding efficiency.
Frequently Asked Questions
Welcome to our guide on exploring the right gas for MIG welding! MIG welding is a popular welding process that requires the use of shielding gas to protect the weld from contaminants and oxidation. In this Q&A section, we will address some common questions about choosing the right gas for MIG welding.
1. What is the purpose of using gas in MIG welding?
In MIG welding, the purpose of using gas is to shield the molten weld pool and electrode wire from the surrounding air. This prevents oxidation and contamination, ensuring a strong and high-quality weld. The gas acts as a barrier, creating a protective environment for the weld.
Additionally, the type of shielding gas used can also affect the characteristics of the weld, such as the penetration depth, bead appearance, and overall performance. Different gases offer different benefits, which is why selecting the right gas is important for achieving the desired results.
2. What are the common types of gases used in MIG welding?
The two most common types of gases used in MIG welding are carbon dioxide (CO2) and argon. CO2 is often used as the primary shielding gas in MIG welding due to its affordability and penetration capabilities. It produces a hotter arc, and deeper penetration, and provides good weld pool control.
Argon, on the other hand, is used as a shielding gas in MIG welding when working with non-ferrous metals, such as aluminum. It provides excellent arc stability and helps create cleaner, smoother welds. Argon is often mixed with other gases, such as helium or carbon dioxide, to enhance specific welding characteristics.
3. How do I decide which gas to use for my MIG welding project?
The choice of gas for your MIG welding project depends on several factors, including the type of metal you are welding, the thickness of the metal, and the desired weld characteristics.
For carbon steel welding, a combination of carbon dioxide and argon is commonly used. Higher percentages of argon are used for welding stainless steel and aluminum.
If you are unsure about the right gas to use, it is best to consult the welding machine manual, seek advice from experienced welders, or reach out to welding supply stores. They can provide guidance based on your specific welding requirements.
4. Can I use pure argon for MIG welding?
Pure argon can be used for MIG welding, but it is typically more suitable for specific applications involving non-ferrous metals, like aluminum. When using pure argon, it is important to adjust the welding parameters accordingly, as it can result in a softer arc and shallower penetration compared to using a mixture of gases.
For welding carbon steel, a mixture of argon and carbon dioxide is often recommended, as it offers better penetration and control. It’s important to consider the type of metal and the desired weld characteristics when selecting the right gas for your MIG welding project.
5. Can I use different gases for different welding positions in MIG welding?
Yes, different gases can be used for different welding positions in MIG welding. The choice of gas can depend on factors such as the welding position (horizontal, vertical, overhead) and the type of joint being welded.
For example, when welding overhead or vertical positions, a gas mixture with higher levels of carbon dioxide might be preferred for better penetration and control. However, it’s important to consult the welding machine manual or seek advice from experienced welders to determine the best gas choice for specific welding positions.
Choosing the right gas for MIG welding is important to get good results. Two common gases used are CO2 and Argon. CO2 is cheaper but can cause more spatter, while Argon is more expensive but produces better weld quality.
It’s essential to consider the type of metal and the desired results when selecting the gas. CO2 works well for steel, while Argon is better for aluminum. So, make sure to choose the gas that suits your specific welding needs.
MIG welding is a versatile and widely used welding technique. By selecting the appropriate gas, you can achieve better weld quality and control spatter. Remember, CO2 for steel and Argon for aluminum. Happy welding!