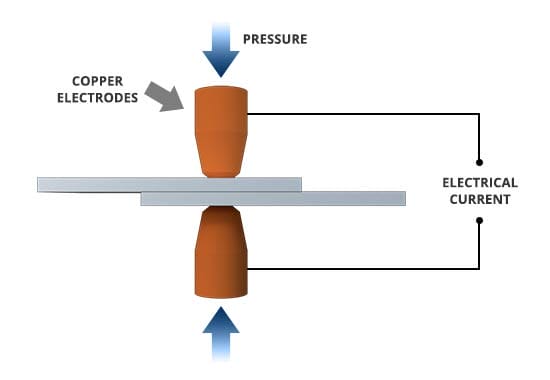
How does a spot welder work? If you’ve ever wondered about the wizardry behind this powerful tool, you’re in the right place! In a nutshell, a spot welder is a specialized machine used to join two metal surfaces together with a strong and permanent bond. It’s like creating a “super glue” for metals!
When it comes to spot welding, there’s no need for bolts, screws, or adhesive. Just a strong jolt of electricity and some clever engineering.
Want to know more about the inner workings of a spot welder? Stick around as we dive into the fascinating world of this high-voltage wonder!
Ready to unravel the secrets of spot welding? Hop aboard as we take a closer look at the amazing process behind this impressive tool. Get ready to discover how electrical circuits, heat, and pressure work together to create a bond that can withstand the test of time. Let’s get started on our electrifying adventure!
Here’s how it works:
1. The spot welder clamps the metal pieces between two copper electrodes.
2. An electric current flows through the electrodes, creating intense heat.
3. The heat melts the metal at the contact point, forming a weld nugget.
4. Pressure is applied to forge the weld.
5. As the weld cools, a strong bond is formed. Spot welders are commonly used in automotive and manufacturing industries for their speed and efficiency.
How Does a Spot Welder Work: A Comprehensive Guide
Here is a video that shows how actually the spot welder works. You can see the video to get a clear idea or you will also find a step by step guide below which explains all the process.
Spot welding is a widely used technique in the automotive, construction, and manufacturing industries. It is a process that involves creating a weld by applying pressure and heat to two metal surfaces.
This article will provide a detailed explanation of how a spot welder works, its components, and the welding process.
Components of a Spot Welder
A spot welder consists of several essential components that work together to create strong and durable welds. The main components are:
1. Electrodes: The electrodes play a crucial role in spot welding. They are typically made of copper alloy and are designed to deliver electrical current to the workpieces.
The electrodes are positioned on either side of the metal pieces to be joined and conduct the electrical current through them.
2. Power Supply: The power supply is responsible for delivering the necessary electrical current to the electrodes. It converts the input voltage into the required output voltage and current for the welding process. The power supply must be capable of delivering high levels of current for a short duration to create effective spot welds.
3. Control Panel: The control panel allows the welder to set and adjust various parameters for the welding process, such as the welding current, weld time, and pressure. It also provides feedback on the welding process, such as temperature readings and weld quality indicators, helping the operator ensure optimal weld performance.
Welding Process
The spot welding process involves several steps that are carefully controlled to ensure precise and consistent welds. Here is a breakdown of the welding process:
1. Preparation: The first step is to prepare the workpieces by cleaning and aligning them. The metal surfaces must be free from dirt, debris, and oil to ensure a clean and strong weld. The workpieces are then clamped together securely, ensuring proper alignment.
2. Electrode Contact: Once the workpieces are properly positioned, the electrodes of the spot welder are brought into contact with the metal surfaces. The electrodes exert pressure, creating a firm connection between the workpieces.
3. Electrical Current Flow: With the electrodes in place and applying pressure, an electrical current is passed through the metal pieces. The current flows from one electrode to the other, passing through the workpieces. The high current density at the interface of the metal surfaces generates heat due to resistance, melting the metal in that region.
4. Melting and Solidification: As heat is generated, the metal at the interface reaches its melting point and starts to melt. The heat also causes the metal to fuse together, forming a weld nugget. The duration of the current flow determines the size and strength of the weld nugget.
5. Cooling: After the welding current is turned off, the weld nugget begins to cool and solidify. The solidification process is essential for the formation of a strong and durable weld. Cooling is typically aided by water cooling systems or other cooling methods to speed up the process and reduce cycle time.
6. Completion: Once the weld has cooled and solidified, the electrodes are retracted, and the workpieces are released. The spot welding process is complete, and the two metal surfaces are permanently joined.
Spot welding is a widely used technique for joining metal surfaces. It involves the use of electrodes to apply pressure and electrical current to create heat, which melts and fuses the metal together.
By understanding the components and the welding process, one can appreciate the complexity and precision involved in spot welding.
Benefits of Spot Welding
Spot welding offers several advantages over other welding techniques, making it a popular choice in many industries. Some of the key benefits include:
1. Rapid Welding: Spot welding is a fast process that can join metal pieces in a matter of seconds. This makes it highly efficient for mass production and assembly line operations.
2. Strong and Durable Joints: Spot welding creates welds that are strong and durable, often matching or exceeding the strength of the parent material. The fusion of metal at the interface ensures a high level of joint integrity.
3. Cost-Effective: Spot welding requires minimal consumables and has low operating costs compared to other welding methods. It is a cost-effective option for industries that require high-volume production.
4. Versatility: Spot welding can be used on a wide range of metals, including steel, aluminum, and various alloys. This versatility makes it suitable for diverse applications and industries.
5. Reduced Distortion: Spot welding creates localized heat, which minimizes distortion and warping in the surrounding material. This is crucial for applications where dimensional accuracy is essential.
While spot welding has its advantages, it is important to consider the specific requirements of each application and choose the welding method accordingly.
Spot Welding vs. Other Welding Techniques
When it comes to joining metal surfaces, different welding techniques have their own advantages and limitations. Let’s compare spot welding with two other commonly used welding methods: MIG welding and TIG welding.
Spot Welding vs. MIG Welding
MIG (Metal Inert Gas) welding, also known as GMAW (Gas Metal Arc Welding), is a popular welding technique that uses a consumable electrode wire and a shielding gas to create the weld. Here are a few key differences between spot welding and MIG welding:
1. Application: Spot welding is primarily used for joining overlapping metal sheets, while MIG welding is suitable for a wide range of applications, including thicker materials and a variety of joint types.
2. Speed: Spot welding is generally faster than MIG welding, as it requires less setup time and can create multiple welds simultaneously.
3. Strength: Spot welding produces stronger and more reliable joints, particularly when joining thin sheet metal. MIG welding, on the other hand, can provide higher strength for thick materials.
4. Heat Input: Spot welding generates less heat compared to MIG welding, reducing the risk of heat-related damage to the surrounding material.
Spot Welding vs. TIG Welding
TIG (Tungsten Inert Gas) welding, also known as GTAW (Gas Tungsten Arc Welding), is a versatile welding process that uses a non-consumable tungsten electrode and a shielding gas to create the weld. Here’s how spot welding differs from TIG welding:
1. Application: Spot welding is typically used for simple joints and production line applications. TIG welding is suitable for precise and intricate welds, such as those required in aerospace or artistic applications.
2. Weld Quality: Spot welding produces consistent and reliable welds, while TIG welding allows for greater control over the weld pool, resulting in a higher level of precision and aesthetics.
3. Heat Affected Zone: Spot welding generates less heat and has a smaller heat-affected zone compared to TIG welding. This is beneficial for applications where minimal heat distortion is critical.
4. Welding Speed: Spot welding is generally faster than TIG welding for basic joint configurations. However, TIG welding allows for better control over the welding speed, making it suitable for complex welds.
It’s important to consider the specific requirements of the project and consult with welding professionals to determine the most suitable welding technique for a particular application.
Tips for Using a Spot Welder
To ensure optimal performance and safety when using a spot welder, here are some useful tips:
1. Proper Maintenance: Regularly inspect and clean the electrodes, power supply, and other components of the spot welder. This helps maintain functionality and extends the lifespan of the equipment.
2. Calibration: Periodically calibrate the spot welder to ensure accurate settings and consistent weld quality. Follow the manufacturer’s guidelines for calibration procedures and frequency.
3. Material Selection: Use the appropriate electrode materials for the metal being welded. Different metals require different types of electrodes to achieve effective welds.
4. Welding Parameters: Adjust the welding current, weld time, and pressure according to the thickness and type of metal being welded. Consult the welding guidelines or seek expert advice if unsure about the optimal parameters.
5. Safety Measures: Always wear proper protective gear, such as welding helmets, gloves, and safety glasses, to protect against sparks, UV rays, and electrical hazards. Ensure proper ventilation in the welding area to avoid exposure to harmful fumes or gases.
By following these tips, operators can maximize the efficiency, performance, and safety of spot welding operations.
Spot Welding in Automotive Manufacturing
Spot welding plays a crucial role in the automotive manufacturing industry, as it is widely used to join various components of vehicles. Here are a few key applications of spot welding in automotive manufacturing:
1. Body Assembly: Spot welding is used extensively in the assembly of car bodies. It is employed to join sheet metal panels, such as the roof, doors, fenders, and trunk, creating a sturdy and rigid structure.
2. Frame Construction: Spot welding is used to join various components of a vehicle’s frame or chassis, including side members, cross members, and reinforcements. This ensures structural integrity and enhances overall vehicle strength.
3. Exhaust System: Spot welding is used in the manufacturing of exhaust systems, joining different sections of pipes and components together. This allows for a secure and leak-free connection.
4. Suspension Components: Spot welding is utilized in the assembly of suspension components, such as control arms, brackets, and linkages. It provides a reliable connection that can withstand the forces and vibrations experienced during vehicle operation.
The use of spot welding in automotive manufacturing ensures that vehicles are built with strong and durable joints, contributing to their safety and longevity.
Spot Welding in Construction
Spot welding also finds applications in the construction industry, primarily in the fabrication of steel structures. Here are a few key uses of spot welding in construction:
1. Steel Fabrication: Spot welding is used to join steel components in the fabrication of beams, columns, trusses, and other structural elements. It provides a fast and efficient method for creating strong connections between steel parts.
2. Reinforcement and Bracing: Spot welding is utilized to reinforce and brace steel structures, such as bridges and high-rise buildings. The welds create rigid connections that enhance the overall stability and strength of the structure.
3. Sheet Metal Joining: Spot welding is often employed in the joining of sheet metal panels used in roofing, siding, and wall cladding. The welds create a secure and weatherproof bond between the panels, ensuring durability and preventing water penetration.
Spot welding offers significant benefits in construction applications, enabling the creation of robust and long-lasting steel structures.
Spot Welding in Manufacturing
Spot welding is a widely used joining process in the manufacturing industry, as it provides efficient and high-quality welds. Here are a few key applications of spot welding in manufacturing:
1. Appliances and Electronics: Spot welding is used in the assembly of appliances and electronic devices, such as refrigerators, washing machines, and computer components. It allows for precise and compact welds in tight spaces.
2. Sheet Metal Fabrication: Spot welding is employed in the fabrication of various sheet metal products, including enclosures, cabinets, and panels. The welds provide secure and aesthetically pleasing joints that meet the high standards of the manufacturing industry.
3. Aerospace Industry: Spot welding is used in the manufacturing of aircraft components and structures. It allows for the joining of lightweight materials, such as aluminum and titanium alloys, with high precision and efficiency.
4. Furniture Manufacturing: Spot welding is utilized in the assembly of metal furniture, such as chairs, tables, and frames. It provides a strong and reliable connection that can withstand the weight and stress applied to furniture pieces.
The versatility and efficiency of spot welding make it an indispensable process in various manufacturing applications.
Spot welding is a versatile and widely used welding technique that offers numerous benefits in various industries. By understanding how a spot welder works, its components, and the welding process, one can appreciate the complexity and precision involved in creating strong and durable welds.
Whether in automotive manufacturing, construction, or general manufacturing applications, spot welding plays a crucial role in creating the structures and products that we rely on every day.
Frequently Asked Questions
Welcome to our FAQ section where we’ll answer some common questions on how spot welders work.
1. How does a spot welder create welds?
A spot welder creates welds by joining two metal surfaces together using heat and pressure. It works by passing a high electrical current through two metal pieces, generating heat at the contact points. The metal surfaces melt and fuse together, forming a solid weld.
Typically, a spot welder has two electrodes that apply pressure to the metal surfaces. When the electric current is passed, the electrodes press against the metal, creating a concentrated heat zone. As the metal cools down, it solidifies and creates a strong weld joint.
2. Are spot welders only used for specific types of metals?
No, spot welders can be used on a wide range of metals, including steel, aluminum, and copper. The ability to weld different metals depends on the power output and design of the spot welder. For example, some spot welders are specifically designed for welding aluminum, while others are suitable for steel or copper.
The key factor is the electrical conductivity of the metal being welded. Spot welders work best on metals with high electrical conductivity, as they allow for better heat generation and penetration. However, it’s important to adjust the settings and parameters of the spot welder according to the specific metal being welded for optimal results.
3. Can a spot welder be used for large-scale industrial applications?
Yes, spot welders are commonly used in large-scale industrial applications. They are particularly useful in industries that require repetitive and high-speed welding processes, such as automotive manufacturing, sheet metal fabrication, and appliance production.
Spot welders are known for their speed and efficiency in creating strong weld joints. With the right setup and equipment, they can produce a large number of welds in a short amount of time.
Additionally, advancements in technology have led to the development of automated spot welding systems, further enhancing their suitability for industrial applications.
4. What safety measures should be taken when using a spot welder?
When using a spot welder, it’s important to follow proper safety precautions. Here are some key measures to consider:
1. Eye protection: Always wear safety goggles to protect your eyes from sparks and potential debris during the welding process.
2. Protective clothing: Wear flame-resistant clothing, gloves, and closed-toe shoes to protect yourself from heat and potential burns.
3. Ventilation: Ensure there is adequate ventilation in the welding area to prevent the accumulation of harmful fumes and gases.
4. Grounding: Make sure the spot welder is properly grounded to avoid electric shock hazards.
Remember to consult the user manual and receive proper training before operating a spot welder.
5. Can spot welds be easily repaired or removed?
Spot welds are generally not designed to be easily removed or repaired. When two metal surfaces are fused together through spot welding, the resulting weld joint is typically strong and permanent. Removing a spot weld often requires cutting or grinding away the welded area, which can damage the surrounding material.
If a spot weld needs to be repaired or removed, it is recommended to consult a professional welder or metal fabricator. They have the expertise and tools to carefully disintegrate the weld and restore the metal surfaces without compromising their structural integrity.
Spot welders are tools that join metal pieces together by creating strong connections through heat. They work by using electrical current to generate intense heat at the contact points, melting the metal surfaces and fusing them together.
Spot welding is commonly used in industries like automotive and construction for its efficiency and reliability in creating secure bonds between metal parts.
By understanding how spot welders work, we can appreciate the importance of this technology in various manufacturing processes. So, next time you see two metal pieces joined seamlessly, remember the spot welder behind it!