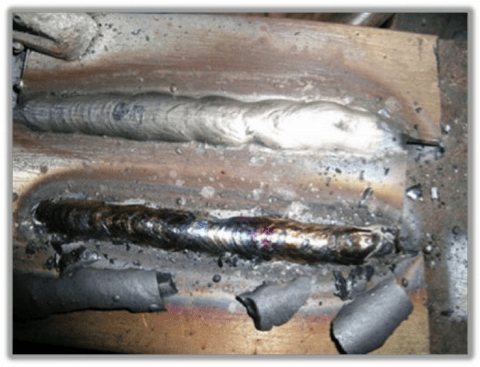
What is Slag in Welding? Well, let me break it down for you in a simple and fun way! When it comes to welding, slag is like the sidekick that helps get the job done. It’s a fascinating and important part of the welding process that you’ll want to know all about.
Imagine you’re building a Lego tower. Sometimes, you might get excess pieces that you don’t need. Well, in welding, slag is a lot like those extra Lego pieces. During the welding process, a protective layer called the flux is used. This flux acts as a shield, preventing impurities and contaminants from ruining the weld. As a result, these impurities get trapped in the flux and form what we call slag.
Okay, so now you know that slag is formed during welding, but what exactly does it do? Well, my friend, slag serves as a protector and cleaner.
It helps keep the weld pool at the right temperature, preventing it from cooling too quickly or overheating. Slag also acts as a barrier, shielding the weld from the air and preventing oxidation. Plus, it helps remove any unwanted debris, making your weld stronger and more durable.
So there you have it, the lowdown on slag in welding. It’s like the trusty sidekick that ensures your welds are top-notch. Now, let’s dive deeper into the world of welding and explore the ins and outs of this fascinating process!
What is Slag in Welding?
Slag in welding is the byproduct created during the welding process. It’s a combination of the flux materials and impurities in the metal. This molten residue floats to the top and forms a protective layer over the weld pool, shielding it from contaminants and preventing oxidation.
Slag also helps to regulate heat and improve the quality of the weld. Understanding the role of slag in welding is essential for achieving strong and durable welds.
Formation and Function of Slag
During the process of welding, when the welding arc is struck and the heat is applied to the parent metal and filler metal, a molten pool is formed.
This molten pool, also known as the weld pool, is the area where the welding actually takes place. As the heat melts the materials, the impurities, fluxes, and other added substances present in the electrode or filler metal also melt and mix with the molten metal. This mixture forms a layer of liquid slag that covers the weld bead.
The formation of slag during welding serves several important functions. Firstly, it acts as a shield or protective barrier, preventing atmospheric gases from contaminating the weld pool.
This protection is essential because exposure to oxygen and other gases can result in defects such as porosity or brittleness in the weld. Secondly, slag helps to slow down the cooling rate of the molten metal, allowing for proper solidification and reduced risk of cracking.
Slag can also act as a deoxidizer and desulfurizer, removing impurities from the weld and improving its overall quality. Overall, slag plays a critical role in ensuring the integrity and strength of the weld.
Composition of Slag
Slag in welding is not a homogeneous substance. Its composition varies depending on the type of electrode or filler metal used and the specific welding process employed. However, certain common components can be found in most types of slag.
One of the main components of slag is the flux material. Flux helps to remove impurities and oxides from the welding area, promoting cleaner and more reliable welds.
Common types of flux materials include limestone, silica, and various metal oxides. Another important component is the shielding gas, which is used in certain welding processes to protect the weld pool from atmospheric contamination.
The shielding gas, such as argon or carbon dioxide, is often released from the welding torch or nozzle during the welding process.
Additionally, slag may also contain elements like manganese, phosphorus, sulfur, and iron oxide, which are present in the welding electrode or filler metal.
These elements can help improve the mechanical properties of the weld and contribute to its overall strength. The exact composition of slag may vary depending on the specific application and desired outcomes of the welding process.
Benefits of Slag in Welding
Slag offers several benefits in welding that contribute to the quality and strength of the weld. One of the significant advantages is its ability to protect the weld pool from contamination by atmospheric gases.
By acting as a shield, slag helps to prevent the formation of defects such as porosity, which can weaken the weld and compromise its integrity. Slag also aids in slowing down the cooling rate of the weld, which reduces the risk of cracking and contributes to a more stable and durable joint.
Another benefit of slag in welding is its role in the deoxidation and desulfurization of the weld. The impurities present in the electrode or filler metal can affect the mechanical properties of the weld, making it weaker or more prone to corrosion.
Slag helps to remove these impurities and ensures a cleaner and more refined weld. Additionally, the presence of certain elements in the slag, such as manganese, can enhance the strength and toughness of the weld, making it suitable for applications that require high durability.
Furthermore, slag can also assist in controlling the shape and appearance of the weld bead. It helps to shape the molten metal and ensures a smooth and uniform weld surface.
This aesthetic aspect of slag is essential in industries where the visual appearance of the weld is essential, such as automotive or architectural applications.
Overall, slag plays a vital role in welding by improving the quality, strength, and appearance of the weld, making it an indispensable component in the process.
Frequently Asked Questions
Welcome to our FAQ section on the topic of slag in welding! Here you will find answers to some common questions about this essential aspect of the welding process.
What is the purpose of slag in welding?
In welding, slag plays a crucial role in protecting the weld pool from external contaminants, such as oxygen and nitrogen. It forms a protective layer over the molten metal, preventing impurities from contaminating the weld. Additionally, slag helps in controlling the cooling rate of the weld, reducing the risk of cracking.
Moreover, slag acts as a flux, facilitating the removal of unwanted elements or impurities from the weld metal. This helps improve the quality and strength of the weld joint.
How is slag formed during welding?
During the welding process, flux is used to protect the weld pool. Flux is a substance that contains various minerals and compounds. When the flux melts, it forms a liquid slag that covers the weld pool. As the slag cools and solidifies, it traps impurities and forms a protective layer over the weld metal.
This slag layer is then removed after the welding is complete. It can be chipped off or removed using wire brushes or specialized tools, revealing the clean weld beneath.
What are the different types of slag in welding?
There are two primary types of slag commonly used in welding: fused slag and flux-cored slag.
Fused slag is created by fusing together a mixture of flux and impurities from the base metal. It solidifies to form a brittle layer on top of the weld, which can be easily removed.
Flux-cored slag, on the other hand, is produced when using a flux-cored welding wire. The flux contained within the wire forms a slag layer during the welding process, providing similar benefits to fused slag.
Can slag affect the quality of a weld?
Yes, the presence and characteristics of slag can have a significant impact on the quality of a weld. If slag is not properly removed from the weld, it can lead to structural weaknesses, porosity, or other defects. Slag inclusion occurs when fragments of slag are trapped within the weld, compromising its integrity.
To ensure high-quality welds, it is essential to remove all slag from the surface of the weld and ensure there are no remnants trapped within the weld joint. Proper cleaning and inspection procedures should be followed to prevent any negative effects caused by slag.
Are there any methods to improve slag removal?
Yes, several methods can help improve the efficiency and effectiveness of slag removal.
One common technique is to increase the welding current, which creates more heat and helps the slag become more fluid, making it easier to remove. Another method involves adjusting the welding parameters to minimize the production of slag.
Additionally, choosing the right type of flux or flux-cored wire can also play a crucial role in improving slag removal. Some fluxes have better slag detachment properties, making cleanup easier. It is essential to follow the manufacturer’s guidelines and recommendations for the specific welding process and materials being used.
Slag is a byproduct of welding that can cause problems if not properly managed. It forms when impurities in the welding process rise to the surface and cool.
Slag can lead to weak welds, corrosion, and difficulties in future welding. To prevent these issues, welders need to clean the slag off their welds using a wire brush or chipping hammer.
Proper cleaning ensures stronger welds and reduces the risk of future complications. If you’re learning to weld, make sure to include slag removal as part of your welding process.